THERMAX’S SMART UTILISATION OF WASTE VAPOUR SAVES HUGE ENERGY COSTS FOR SNACK MANUFACTURER
- coolingcommunicati
- Feb 24, 2020
- 3 min read
What’s waste for you, will not only give you free cooling, but will also…
Sustainable productivity, a buzzword across industries today, has become the top agenda of businesses across the globe. Fuelled by cutting edge technology, backed by innovation and digitalisation, the impulse of achieving energy efficiency is skyrocketing.
With the increasing demand for potato-based snacks across the globe, large to small scale manufacturers aim to boost their productivity, quality, and sustain their brand credibility. The look-out for sustainable productivity, operational excellence, and profitability are paving the way towards solutions that can be answers to the requirements of these industries.
Thermax, with a strong commitment towards improving processes and helping customers achieve operational excellence, has provided an innovative and unique solution to potato-based snack manufacturers across the globe including the world’s largest potato chips producer with manufacturing units in India, United States, Thailand, Saudi Arabia, and Mexico.
Harnessing waste heat, the innovative way!
Potato has nearly 70% water content! Upon frying, the water gets converted into low-pressure vapour which is released into the atmosphere using an induced draft fan in the chimney. Thermax’s absorption chiller utilizes this vapour to provide air conditioning in the production area of the facility which would otherwise require a power of about 350kW using an electric chiller. In addition to this, the condensate from the absorption chiller is used for washing raw potatoes resulting in zero water discharge. This has not only encouraged the manufacturers to make an energy-saving cooling choice but has also shortened the payback period.
Thermax’s innovative solution for potato snack manufacturers
After the washing and before the frying processes, potatoes go through a series of intermediate processes such as peeling, arranging, blanching, slicing, and dehydrating. Thermax’s Ultra Low-Pressure chiller is placed right after the frying process. The low-pressure vapour formed from the frying of potatoes has a temperature of approximately 115°C and a pressure of about 0.3kg/cm2. This low-grade vapour is used as a heat source in our chillers to give chilled water of the desired requirement. The condensate recovered from the chiller is accumulated and is used for cleaning the potatoes thereby saving an enormous quantity of water annually.

Advantages of Thermax ULP Vapour Absorption Chiller
Thermax’s Ultra low-pressure vapour absorption chiller not only saves electricity, but also saves the requirement of an external/additional heat source; amounting to zero power consumption and a shorter payback period.
The innovative solution complies with the Kyoto Protocol, thus protecting the planet in alignment with the sustainability goals of the organization globally.
Eliminating CO2 emissions and with no use of CFCs, this Vapour Absorption Machine becomes an environmental friendly chiller.
The condensate which is reused to wash the potatoes saves an enormous amount of water.
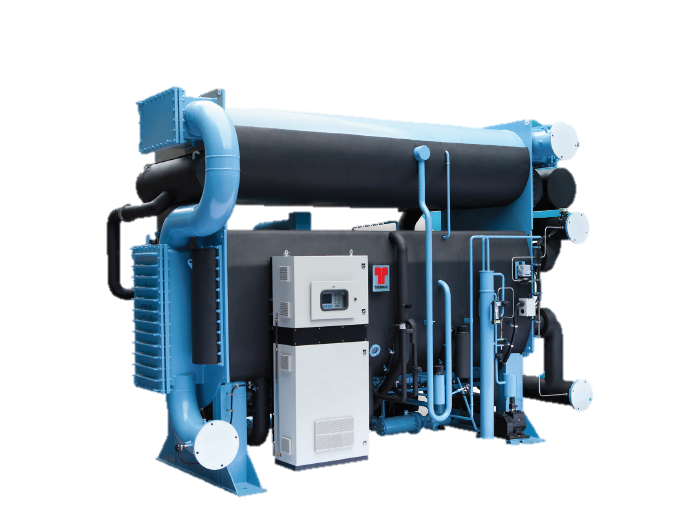
A typical Ultra low-pressure vapour absorption chiller can provide a cooling capacity ranging from 40TR to 3000TR
What’s waste for you, will not only give you free cooling, but will also…
… Provide you with
Power Savings: nearly 3 million units annually
CO2 Reduction: 4000 tons annually
Water savings: 24000 m3 annually
Note: Calculated for a typical 600TR machine installed in the world’s largest potato chips manufacturing unit.
Thermax’s Absorption Cooling & Heating Division: At a glance
With over 50 years of expertise in the field of Thermodynamics, Thermax absorption chillers cater to industrial cooling, commercial air conditioning as well as industrial and space heating needs. Thermax’s USP lies in identifying the unused heat available at manufacturing units and provide recovery based or live energy-based solutions to optimize energy thus reducing the operational cost.
The Absorption Cooling & Heating division of Thermax offers solution from -400F to 3560F i.e. -400C to 1800C by using hot water starting from 1760F (800C) or from steam or vapour from 0 psi(g) onwards or flue gases from engine and turbines from 5180F (2700C) onwards and a variety of liquid and gaseous fuel.
Over these years, Thermax has helped clients with eco-friendly air-conditioning and process cooling to reduce their carbon footprints. Thermax has a strong global footprint extending to more than 90 countries across the world.
For more information about the Absorption Cooling & Heating division and its innovative and sustainable solutions, visit https://www.thermaxglobal.com/thermax-absorption-cooling-systems/vapour-absorption-machines/triple-effect-chillers/
Comments