THERMAX’S ROSS SIMPLIFIES MACHINE MONITORING AND CORRECTIVE MAINTENANCE AT ADAM AFRIQUE
- coolingcommunicati
- Apr 16, 2020
- 3 min read
Adam Afrique
Adam Afrique is a well-known producer of soaps in the west African country, Ivory Coast. Situated in the industrial zone of the capital city, Abidjan, it is a Limited Liability Company established in 1987. The company uses locally available natural resources to manufacture soaps of exceptional quality. With a rich range of products covering all household needs, the company’s clientele list extends overseas beyond the domestic market.
The latest industrial development and the availability of locally sourced palm oil and coconut oil in the Abidjan region have made it an attractive spot for soap manufacturers. Several soap manufacturers thrive in the area catering to the country’s domestic and export needs. Since the intensity of the competition is high, keeping up the productivity of the soap-manufacturing unit every day is vital for Adam Afrique.
Thermax’s chiller at Adam Afrique
Aligning with the company’s interests to increase production, Adam Afrique collaborated with Thermax to meet the cooling requirements of the saponification process in its plant. On 13th November of 2018, Thermax commissioned a double-effect steam fired vapour absorption chiller of 360 TR capacity at their plant. The chiller runs on steam exhaust of a plant process and caters to the cooling section of the saponification process. The chiller has been performing well by delivering chilled water at 10°C since its commissioning. To ensure uninterrupted operation and predictive maintenance, the chiller is connected to Thermax’s cloud-based remote monitoring technology, ROSS (Remote Online Service Support).
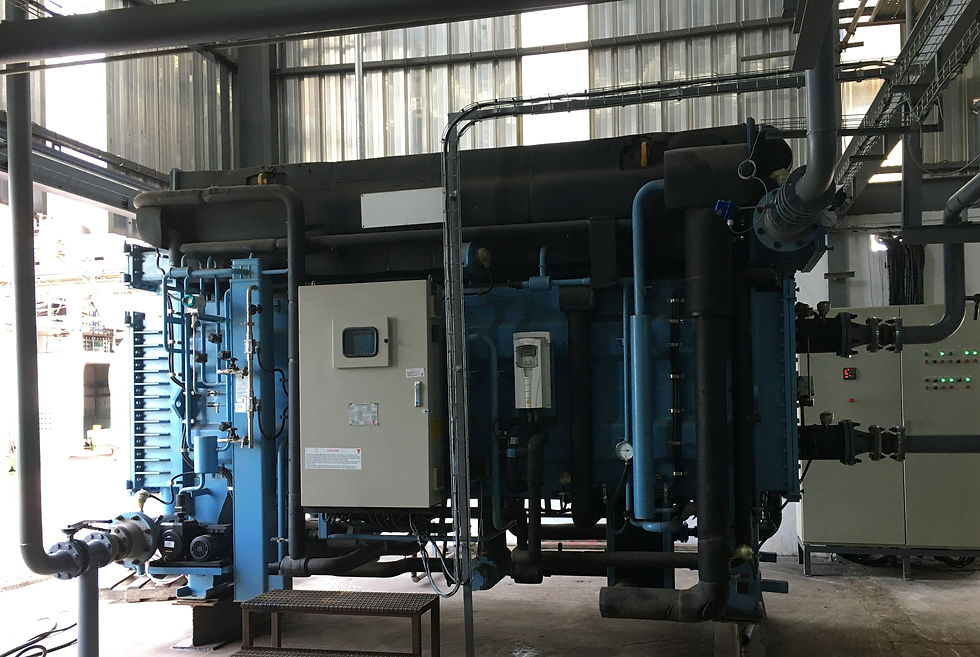
Machine Monitoring Without Site Visit in Real Time
On 7th April 2020, an operational issue was observed in the chiller at the plant of Adam Afrique. Our technical service team intervened and logged into the chiller. After a study of the chiller’s latest data logs, a photograph of the recorded parameters on the machine’s HMI was requested. Through ROSS, our service engineer was able to monitor the performance of the machine even when it was running. Anticipating a vacuum break in the chiller, our service team instructed the plant operator to perform a vacuum test.
Nitrogen gas at 0.2 bar was charged into the chiller and the test was conducted. The initial pressure at 25mm Hg dropped to 90mm Hg within 12 hours, confirming a leakage in the chiller. The post-detection maintenance measures were communicated remotely to the plant operator. The leak was attended temporarily by fixing with metallic potty and then LiBr was charged into the chiller. After closely monitoring the chiller for 24 hours, the chiller’s operations were declared normal. The timely response and proactive maintenance service by our service team ensured a continued operation at the soap manufacturer’s plant.
Issue Analysis and Preventive Maintenance to Reduce Downtime
Further analysis to identify the root cause of the issue found that the line of the cooling water inlet and outlet were below the required size at the plant. It was also found that the cooling water temperature in the chiller went as high as 35°C as opposed to the designated 32°C. The root causes were communicated to the customer and the corrective measures to fix them were suggested as well.
ROSS’s excellence building deeper customer relationships
The chiller issue that sprang up unexpectedly, in a very crucial moment put the company’s productivity at stake, especially as the production process at their plant is kept up on toes by the competitiveness in the market. ROSS helped the company keep up its pace by providing accurate operational data and remote maintenance.
Highly satisfied with the chiller’s performance, ROSS’s reliability, and the exceptional service experience, Adam Afrique has decided to adopt our chillers again in view of their plant expansion.
Mr. A. Mahmoud, the Deputy Technical Director at Adam Afrique says,”On behalf of Adam Afrique team, our thanks to Thermax team, for the professionalism displayed throughout this project right from project initiation, delivery commitment, installation support to start up.”
ROSS – Continuous Monitoring with An Automated Solution
At Thermax, addressing every conceivable factor of customer experience is crucial. Our efforts to offer excellent service coupled with the recent advancements in remote automated solutions gave way to ROSS. ROSS is a system of cloud-based industrial maintenance which connects installations across the globe to Thermax’s servers. ROSS enables managing and monitoring the chillers with alarms, trend graphs, and reports efficiently. With ROSS, the exact status of the chiller can be monitored anytime thus offering customer service and chiller maintenance remotely. Machines across the globe can be promptly serviced by engineers remotely at the slightest indication of deviation in its parameters. The system, apart from speeding up the troubleshooting process, completely avoids the chiller’s downtime and call for maintenance.
With ROSS, the chillers’ operations and parameters are constantly monitored and actions for efficiency improvement are recommended to the operators at the plant. The operators are contacted on time to prevent unnecessary disruptions of the plant operations.
Comments