THERMAX’S REMOTE MONITORING SERVICE PREVENTS DOWNTIME AND MAINTAINS PRODCUTIVITY AT CBL GLOBAL FOODS
- coolingcommunicati
- May 15, 2020
- 3 min read
CBL Global Foods Ltd, manufacturer and exporter of coconut-based products, is a group company of the legendary Ceylon Biscuits Limited in Sri Lanka. The company is known well in the country for its ‘Sera’ coconut milk, organic coconut milk, coconut water and juices. Being a primary exporter of coconut products to Europe & Asian countries, CBL Global Foods Limited has in place a sophisticated plant dedicated to steam infusion and downstream homogenisation process.
Thermax’s chillers at CBL Global Foods
With the island nation implementing stringent legislation and standards for the food industry, CBL Global Foods introduced a few changes to their food processing operations. As a part of the revamp, the company replaced its cooling machinery with two of Thermax’s steam fired vapour absorption chillers each of 98 TR capacity. The chillers cater to the process cooling of coconut milk in pasteurizers and comfort cooling at the plant. Regarding the chillers, “We are glad to record that since their erection from 2015 onwards, the chillers are in continuous operation to cater to the plant’s chilling load and we are satisfied with the efficiency and performance of the machines”, says Gihan Samaraweera, Assistant Engineering Manager at CBL Global Foods. The chillers are connected to ROSS (Remote Online Service Support) because of which they are under constant monitoring by Thermax’s service team.
Spotting potential problem in the chiller
On the morning of 17th August of 2019, ROSS displayed a temperature deviation in the chiller at CBL Global Foods’ plant. The outlet temperature was at 6.8°C against the designated 2°C. The defect, if left unnoticed would have led to an inevitable loss of productivity since cooling is an important procedure in coconut milk processing. Our technical service team logged into the chiller and analysed its previous data logs. The ROSS reports traced back the issue to irregular purging and blowdown of the machines. Failure to perform blowdown in the chillers often results in slow down of operations. In addition, the inlet cooling water was sent at a temperature higher than the designated 7.1°C.
The issue was communicated to the operator and addressed on the same day. Towards the evening of 17th August, the chiller’s outlet temperature was brought down to 1.8°C against a setpoint of 2°C. The temperature deviation possessed the potential to result in a 3-day downtime of the plant’s processes. Detection of aberration in the chiller parameters and identification of the root cause well in advance prevented unwanted downtime and huge maintenance costs to the company. Quick intervention by the service team with accurate information at the right time led to an uninterrupted production process at CBL Global Foods. Speaking on ROSS, “We also like to express our appreciation to their Technical Services team for providing digital services via Internet with their innovative and advanced technology. In the past one and a half years, their smart services had helped us maintain 100% uptime of the machines. We are excited and pleased to use this facility and would recommend ROSS to other organizations using Thermax Absorption Chillers”, added Gihan.
CBL Global Foods having experienced the benefits of ROSS several times appreciated Thermax’s Technical Service team for their timely support. ProiCare analytics from ROSS sends automated mails of the daily data logs, fortnight reports, and other alerts, which helps the company maintain a 100% uptime of the machines. Addition of ROSS to the commissioned chillers gives Thermax the opportunity to collect data, check status, predict down-time, recommend solutions and do so much more that industries using chillers never know exist. Service with ROSS at CBL Food Groups is another epitome of how Thermax takes customer service to incredible heights.
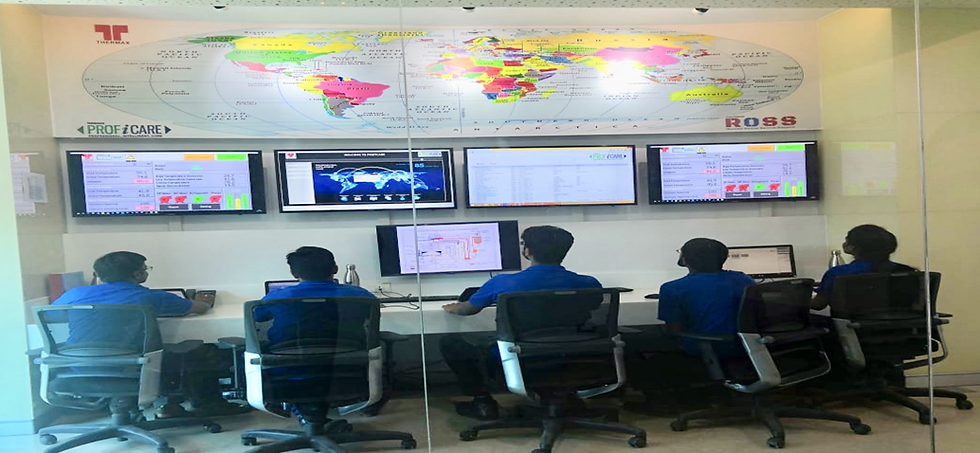
ROSS – Continuous Monitoring with An Automated Solution
At Thermax, addressing every conceivable factor of customer experience is crucial. Our efforts to offer excellent service coupled with the recent advancements in remote automated solutions gave way to ROSS. ROSS is a system of cloud-based industrial maintenance which connects installations across the globe to Thermax’s servers. ROSS enables managing and monitoring the chillers with alarms, trend graphs, and reports efficiently. With ROSS, the exact status of the chiller can be monitored anytime thus offering customer service and chiller maintenance remotely. Machines across the globe can be promptly serviced by engineers remotely at the slightest indication of deviation in its parameters. The system, apart from speeding up the troubleshooting process, completely avoids the chiller’s downtime and call for maintenance.
With ROSS, the chillers’ operations and parameters are constantly monitored and actions for efficiency improvement are recommended to the operators at the plant. The operators are contacted on time to prevent unnecessary disruptions of the plant operations.
Comments