SALALAH MILLS KEEPS UP ITS PRODUCTION RATE, THANKS TO ROSS
- coolingcommunicati
- Dec 24, 2020
- 3 min read
Based in Oman, Salalah Mills Co. (SMC) is one of the largest flour producers in the Middle East. SMC is a leading supplier of different grades of wheat flour and wheat products like semolina, animal feed pellets, wheat bran, etc. The company’s markets expands beyond Oman into many other African countries, pushing its production capacity to 1,500 tons per day. To sustain the production rate, Salalah Mills employs modern state-of-the-art-technology milling equipment and processing utilities.
Salalah Mills had partnered with Thermax in 2012 for a cooling solution for its plant in the national capital, Muscat. The exemplary performance of the 250 TR chiller and our service support prompted the company to collaborate with Thermax again. A repeat order was placed for a 320 TR direct fired absorption chiller, which required immediate commissioning to ensure operational continuity at the plant– a challenge in view of the travel restrictions in the country.
CRITICALITY OF CHILLER IN PRODUCTION
Commissioning of the chiller was crucial to the plant operations, considering its dual application in cooling the admin block and pasta production. Since the pandemic travel restrictions were still in place, site visits to the plant were beyond the scope. To prevent any productivity loss at the mills, Thermax suggested online commissioning of chiller to the flour company.
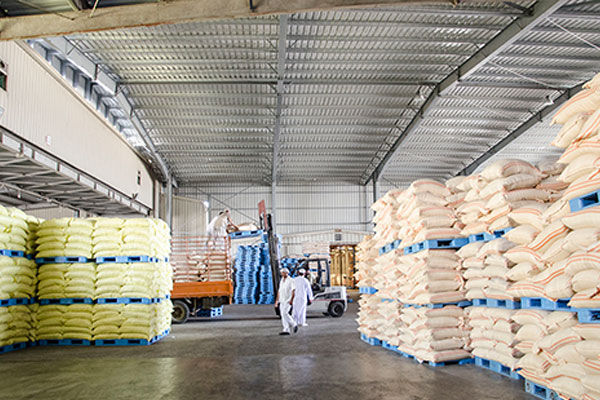
“ROSS TO THE RESCUE” IN TROUBLED TIMES
The technical services team from Thermax took control of the chiller equipment remotely via Remote Online Service Support (ROSS). The service expert assisted the commissioning by continuously monitoring the procedure far from the plant. With the team’s constant virtual guidance, the equipment was successfully commissioned. Our expertise in remote commissioning of chillers across the globe led to a smooth and effortless installation at Salalah Mills. Performance qualification tests were run soon after and the chiller parameters were found to be optimal.
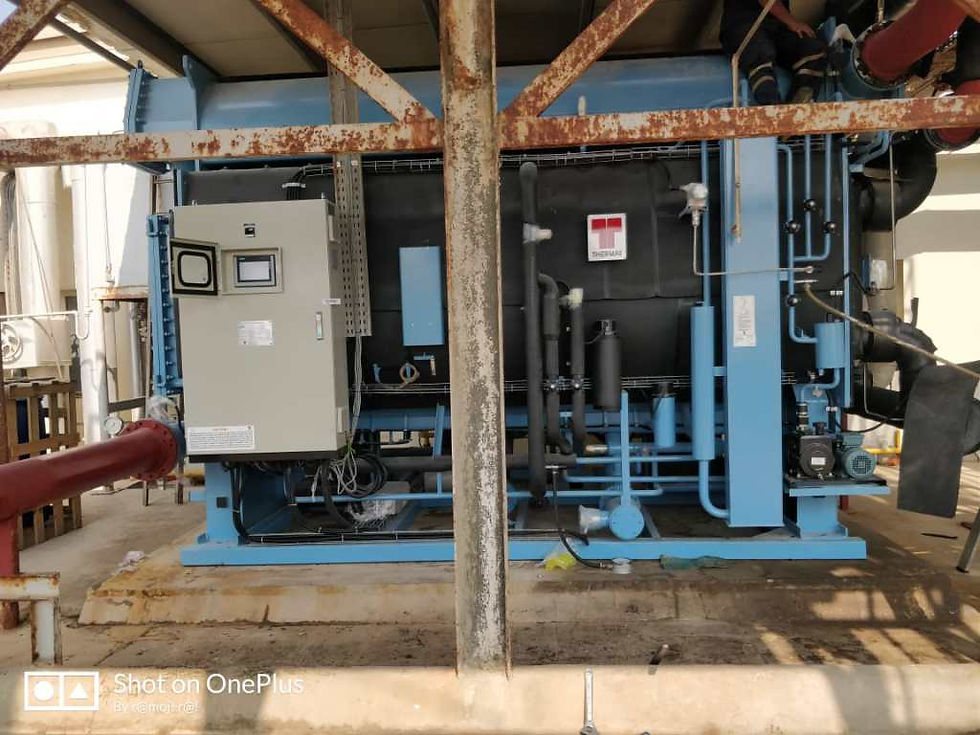
LEVERAGING IIoT TO KEEP UP PRODUCTIVITY
The chiller was immediately put to operation in the plant. The chilled water caters to the comfort cooling of the plant’s admin unit and also cools the pasta during production. Despite being not physically present on-site, our expert, leveraging the usefulness of ROSS, ensured that no loss of productivity was incurred at Salalah Mills. Post the commissioning, the chiller is still connected with ROSS and is under continuous monitoring.
“As we were in a very critical situation to commission the chiller to meet our production demand and it was not possible for Thermax’s service person to be physically present due to Covid pandemic, the service team team with much dedication, successfully commissioned the unit remotely & met our process need and comfort cooling requirement on time. With the help of the ROSS platform, the chiller is also now connected online monitoring and we are getting adequate information through it” says Augustine V Manuel, Projects and Maintenance Manager at Salalah Mills.
As the pandemic continues to present a serious threat to operational continuity in industries, Thermax’s ROSS as a new way of service support has enabled customer success in these challenging times. ROSS has demonstrated its value on many occasions over the years, now more so during the pandemic. Amidst the travel restrictions, the cloud-based IIoT has rendered it unnecessary to rely on in-person support to minimize the impact on production.
ROSS – CONTINUOUS MONITORING WITH THE CLOUD-BASED IIoT
At Thermax, addressing every conceivable factor of customer experience is crucial. Our efforts to help customers sustain productivity with the recent advancements in industrial IoT gave way to ROSS. ROSS is a system of cloud-based industrial maintenance which connects chiller installations across the globe to Thermax’s servers. ROSS enables managing and monitoring the chillers with alarms, trend graphs, and reports efficiently. With ROSS, the exact status of the chiller can be monitored anytime thus offering customer service and chiller maintenance remotely. Machines across the globe can be promptly serviced by engineers remotely at the slightest indication of deviation in its parameters. The system, apart from speeding up the troubleshooting process, completely avoids the chiller’s downtime and call for maintenance.
With ROSS, the chiller’s operations and parameters are constantly monitored and actions for efficiency improvement are recommended to the operators at the plant. The operators are contacted on time to prevent unnecessary disruptions of the plant operations.
留言