Preventive Care: Nitrogen Blanketing
- coolingcommunicati
- Jan 18, 2016
- 3 min read
One of the most important aspects of preventive care in absorption chillers is ‘preservation’. This is ignored many times resulting in frequent issues due to corrosion, loss of efficiency and shortening of the service life of the equipment.
The most critical breakdown in a chiller apart from component failure occurs when the vacuum breaks either due to tube ruptures, leaks or if there is any physical reason for ingress of air in the machine such as leaks through the service valves or gland, leaving the purge valves open allowing air to enter the chiller or leaving the machine open during any repair or maintenance work.
As Lithium Bromide (LiBr) is highly corrosive in the presence of atmospheric oxygen, the corrosion process starts. It is therefore important that in such situations quick actions are initiated to seal off the leaks temporarily and keep the machine under an inert nitrogen atmosphere until a permanent action is initiated.
One of the common mistakes most technicians do after sealing off the leaks in the tubes or welding of the chiller is that they quickly charge nitrogen in the machine and declare that the machine is safe under preservation.
This should be strictly avoided as there is atmospheric air already present inside the chiller. This is because during the leak either air or water containing atmospheric oxygen enters the chiller through the leaking area and gets trapped in the chiller. It is therefore important to realise this fact.
Charging the machine with nitrogen only increases the pressure of the air inside the shell. Since this trapped air inside the chiller shell contains oxygen, the process of corrosion gets initiated. Hence in such situations it is extremely important that only after the leaking areas are sealed off with reasonable strength such as plugging, welding etc. that a vacuum is created in the machine by running the vacuum pump and pulling out all the entrapped air.
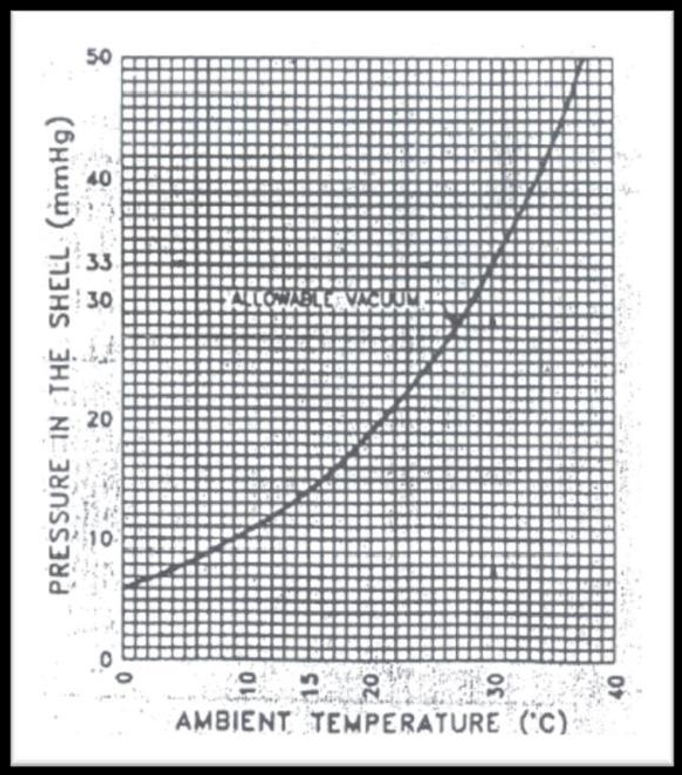
On reaching this attainable vacuum,(refer chart for attainable vacuum to be pulled w.r.t the ambient temp prevalent at the time of purging) the chiller should be kept under the vacuum hold test for at least 12 hours and checked for vacuum drop. In case a drop in vacuum is observed, the chiller should be rechecked for leaks and such leak should be attended and the process repeated till the attainable vacuum and vacuum hold test is achieved.
Only then should the machine be charged with nitrogen so that the gas fills up the entire shell and an inert nitrogen atmosphere is achieved. At no point should the chiller be left unattended allowing air to stay for long inside the chiller. This is also applicable for any normal long or short duration shutdowns when the chiller is taken out of service. A proper de-commissioning procedure should be performed to ensure trouble-free operation and longer life of the equipment.
(article by Cooling-Services)
Comments