PHARMACEUTICALS MAJOR IN NIGERIA COLLABORATES WITH THERMAX FOR ELECTRICTY-FREE COOLING
- coolingcommunicati
- Aug 3, 2020
- 2 min read
A well-known pharmaceutical company in the medical fraternity of Nigeria, established in 1987 began with specifically manufacturing intravenous fluids. Over the years, the company has begun producing a range of products such as analgesics, anti-hypertensives, anti-diabetics, and dermal preparations etc.
The pharma company has stayed atop the industry owing to its continual commitment and strict adherence to quality products and processes. It employs innovative and high-tech manufacturing processes beneficial for the company’s bottom line. In line with its commitment, the pharma giant has deployed three Thermax chillers to comfort cool its production floors.
CRITICAL REQUIREMENT OF ELECTRICITY-FREE COOLING
As Africa’s largest economy and the biggest consumer market, Nigeria has been hailed as the best frontier for pharmaceutical industry in the continent. But the issue of power outage in the country casts an altogether different light on the industry’s prospect. The energy crisis hits industrial operations and takes a harsh toll on the productivity and hence on the economy of businesses.
Due to the frequent power failure, there is a constant risk of disruption in manufacturing and discomfort to workers on the production floors. The grid is so unreliable that the industries follow a trend of investing into zero-electricity solutions and utilities. Facing the energy crisis, the pharma major was looking for a prospective cooling solution that runs without electricity while improving the productivity of the plant.
PUTTING COST OPTIMISATION IN PERSPECTIVE
Combating the unreliability of power grid, the company has an on-site own captive power plant (Generator). In a position to rely on fuel sources other than electricity which can optimise costs simultaneously, the company zeroed upon Absorption Chiller as the ideal cooling solution.
Thermax’s leading know-how and expertise combined with our successful installations in other African countries led to this collaboration. Visits to Thermax’s other installations in the country enabled the customer to evaluate the benefits of chillers and their operational insights. Feasibility study involving an in-depth inspection and analysis of the heat source followed the visits.
OFFERING ZERO-ELECTRICITY CUSTOMISED COOLING SOLUTION
Reducing the company’s energy costs was what the Thermax team set out to do when the first direct fired chiller of 200 TR was commissioned at the pharma plant in 2007. Following the reduction in energy costs and realization of chiller benefits, the company sought the same cooling solution again as a part of their plant expansion in 2015.
Our service excellence and efficient means of chilling have had Thermax commission 3 direct fired chillers in the pharma plants so far – all driven by natural gas and Diesel.
The three machines are employed to cater to the comfort cooling demands of the production area. Chilled water from the absorption chillers maintain the room temperature constantly at around 24°C, thus improving the comfort and productivity of workers. Apart from improving reliability, the chillers have helped the pharma manufacturer reduce its CO2 emissions associated with electricity generation.
THERMAX’S CHILLERS BRING THE FOLLOWING BENEFITS TO THE PHARMA COMPANY
Thermax has been transforming industrial heating and cooling by taking the applications off the grid. By eliminating electricity from the scene, we enable industries to explore alternative energy sources and benefit from enormous energy savings.
The three direct fired absorption chillers at the Pharmaceuticals plant ensure seamless operation while offering several energy benefits to the company.
PRODUCT FEATURES
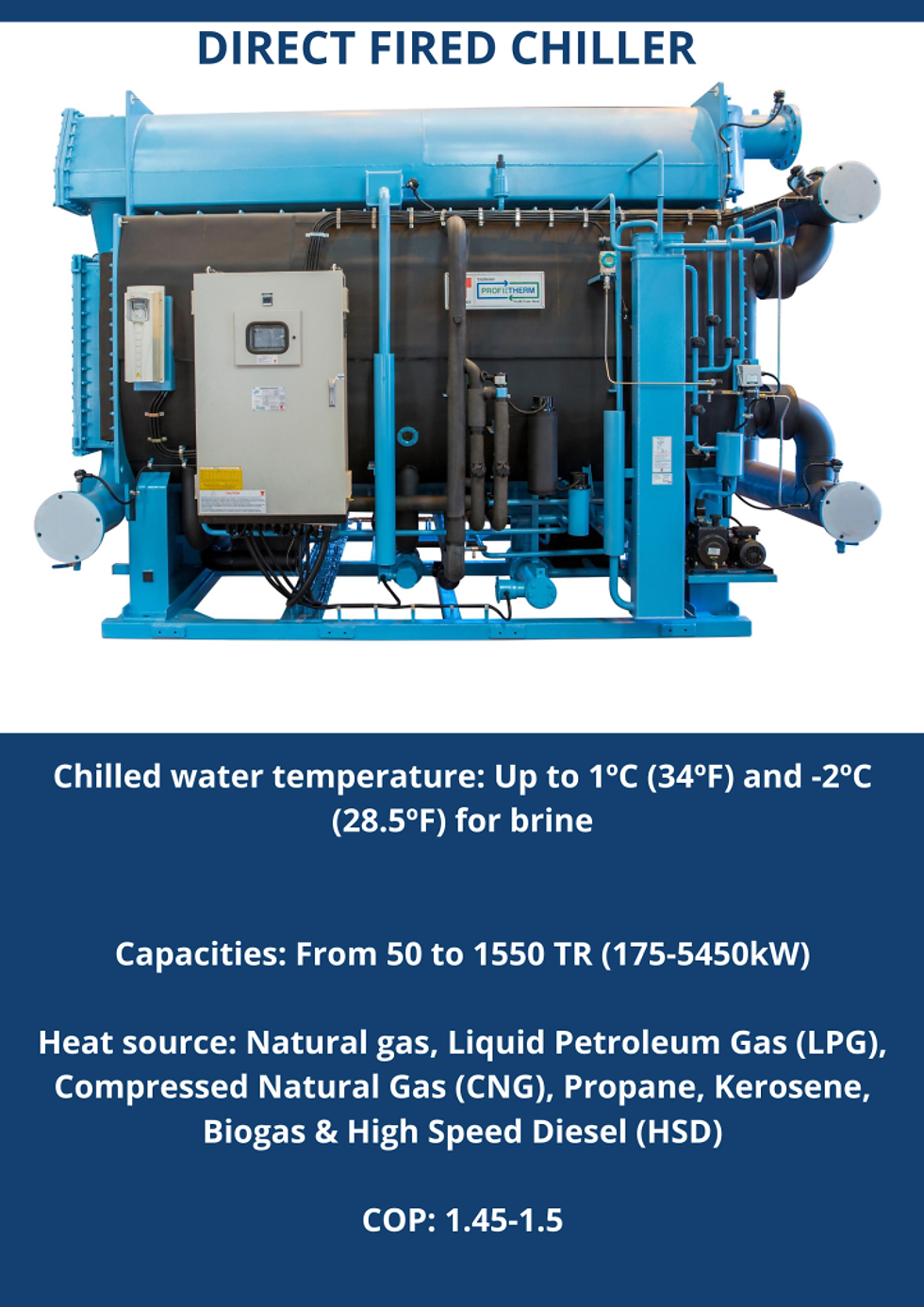
Comments