ENHANCING ENERGY EFFICIENCY IN FOOD PROCESSING INDUSTRIES WITH ABSORPTION TECHNOLOGY
- coolingcommunicati
- Jul 22, 2020
- 3 min read
Updated: Aug 3, 2022
Increasingly, the food industry plays an important role in feeding the growing population while meeting the food quality standards. Energy is a significant input cost for the industry considering the energy-intensive manufacturing and processing systems.
Cooling and heating systems (dryers, ovens, furnaces, and refrigeration units) have the highest energy requirements in food manufacturing facilities. Rising energy costs, surging demand, and environmental consciousness have motivated food manufacturers to develop processing systems that reduce energy consumption and release fewer emissions.
Absorption Cooling and Heating technology presents itself as the right solution for the energy challenges faced by the industry. Vapour absorption machines are electricity-free cooling and heating units with very low operational costs. They also come with the potential to run on heat recovered from the facility’s existing processes or utilities, thereby reducing GHG emissions to a sustainable level.
TRANSFORMING ENERGY UTILISATION IN DAIRY PROCESSING
Modern processing equipment in the dairy industry accounts for about 40% of its total energy consumption. Vapour absorption machines, when employed for chilling, pasteurization, and storage can offer huge operational and energy savings. Read more at: https://bit.ly/3Q34vI8
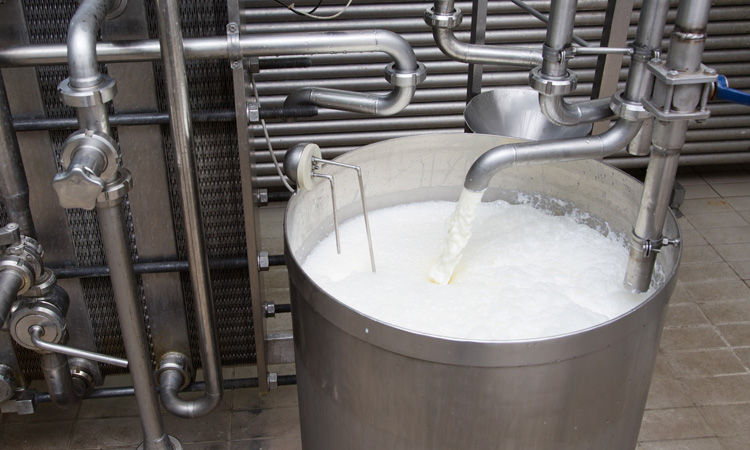
CAPTURING ENERGY AT FRIED FOOD PRODUCTION
Fried-snacks manufacturers have a huge potential to employ vapour absorption technology in conjunction with several heat recovery opportunities. Thermax’s unique cooling application to a leading potato-snack manufacturer runs on waste heat from the plant and caters to its comfort cooling requirement, thus significantly impacting the company’s bottom line. Read more at: https://bit.ly/3Skxqc1

OPTIMISING THE REFINING PROCESS OF EDIBLE OIL
Edible Oil undergoes extensive refining phases including Solvent Extraction and Oil Cooling. Vapour absorption machines employed in the refinery line can remarkably minimize the energy consumption and drive down operations costs in the refinery units. Read more at: https://bit.ly/3Jv1rll

ENERGY OPTIMISATION AT NOODLES MANUFACTURING
The noodle manufacturing line involving the steamer, boiler, and dryer is energy-intensive and generates excessive waste heat. Energy optimisation in the industry can be realised by integrating vapour absorption machines along with heat recovery systems. Read more at: https://bit.ly/3P0mnSq

MEETING COOLING DEMANDS OF COCONUT PROCESSING INDUSTRY EFFICIENTLY
Coconuts are processed for various products such as water, milk, cream, oil and more. Coconut processing industries require advanced cooling technologies for processing and preservation. The extracted coconut water, after filtration must be cooled down in order to avoid microbiological and chemical reactions, which cause color and structural changes. For an industry with very high cooling energy demand, absorption technology is the prospective cost-effective solution for energy-efficient cooling. The absorption cooling machines, customized to various cooling temperature requirements for different processes offer operational savings coupled with environmental benefits.

PROCESSING AND PRESERVING FRUIT JUICE IN THE MOST SUSTAINABLE WAY
Fruit Pulp processing is a fast-growing industry owing to the increased consumer preference for healthy food. In the process of making regional fruits available all over the globe, the industry adds economic value to fruits and eliminates the losses associated with unprocessed fruits. Climacteric fruits, such as peach, apple, mango, guava, passion fruit, among many others, are used for pulp extraction. Majorly directed at exporting, the fruits undergo a variety of processing and preserving procedures to extend their shelf life.
Energy utilisation for processing and preserving the fruits constitute a big challenge for pulp processing industries. The processes involved focus mainly on conserving the physical structure and the nutritional value of the fruits. The pulp is heated up to 70°C and then cooled down to room temperature. The cooling temperature depends on the country’s climate and shelf-life demands – even up to 20°C. Since fruit processing units employ wood-fired boilers, steam is available in plenty at the site. Capturing the steam from the boilers, double-effect steam fired absorption chillers can be the energy-efficient cooling solutions for fruit processing industries.

ความคิดเห็น