ENHANCING EFFICIENCY IN YARN MANUFACTURING WITH CUSTOMIZED COOLING SOLUTION
- coolingcommunicati
- Nov 20, 2020
- 2 min read
A well-known yarn manufacturer in the textile processing industry of Bangladesh who specializes in the production of cotton yarns for knitting and weaving has over six manufacturing units across the country. Its product profile flaunts a wide range of specialty and superior-grade yarns which make up a significant proportion of Bangladesh’s fabric exports.
The yarn manufacturer deploys a sophisticated range of automated equipment in its spinning mills. Modernised equipment and continuous usage of the machines essentially increase the company’s operational costs. Focusing on energy optimisation, the mills have their own IPP generating power and use waste heat to cool the factory. As a part of the company’s efforts towards energy conservation, Thermax’s cooling solutions have been integrated with the mills’ processes and continue to provide healthy margins to the textile manufacturer while improving its productivity.
IMPORTANCE OF COOLING IN SPINNING MILLS
Cooling application in spinning mills is critical for enhancing the processes and products involved. Yarn properties like dimension, tensile strength, elastic recovery, and rigidity are greatly influenced by moisture regain, which is controlled by the humidity and cooling conditions of the mill. While any slight deviation in the humidity and cooling temperature can go as far as stopping productions, creating discomfort to the workers, and damaging machinery, getting the temperature right can maximize product weights, improve quality, and accelerate machine speed. Hence, the humidification plant alone utilises 14% of the total energy consumed in a spinning mill. Ideally, the cooling application in a humidification plant holds the major power saving potential in a mill.
THERMAX’S EXPERTISE IN COOLING MILLS
Thermax holds the distinction of introducing Absorption chillers in Bangladesh. For several years, Thermax has been enabling quality production and energy savings for industries of all sorts and sizes in the country. Our previous offerings for spinning mills across the globe combined with the proactive service support led the yarn manufacturer to collaborate with Thermax for meeting its cooling requirement.
ENERGY-EFFICIENT COOLING SOLUTION OFFERED
As an energy-intensive industry, the mills generate their own power on site. A 40 MW gas engine based capacitive plant serves as the physical hedge to lock in the cost of power. Consequently, the mills had free heat available from the power plant, which could be reused in line with complete capacity utilisation.
The textile company was seeking energy-efficient solutions for cooling in its polyester chip factory. Thermax has commissioned nine Exhaust and Jacket water driven chillers each of capacity 458 TR at the mills. They are driven by the exhaust heat from the gas engines. With the commissioned chillers that basically run with zero-cost heat source, energy utilisation trend of the mills has been transformed tremendously. Our solutions apart from cooling the manufacturing process have reduced the plants’ electricity consumption to a great degree.
KEY BENEFITS REALISED WITH THE COMMISSIONING OF CHILLERS
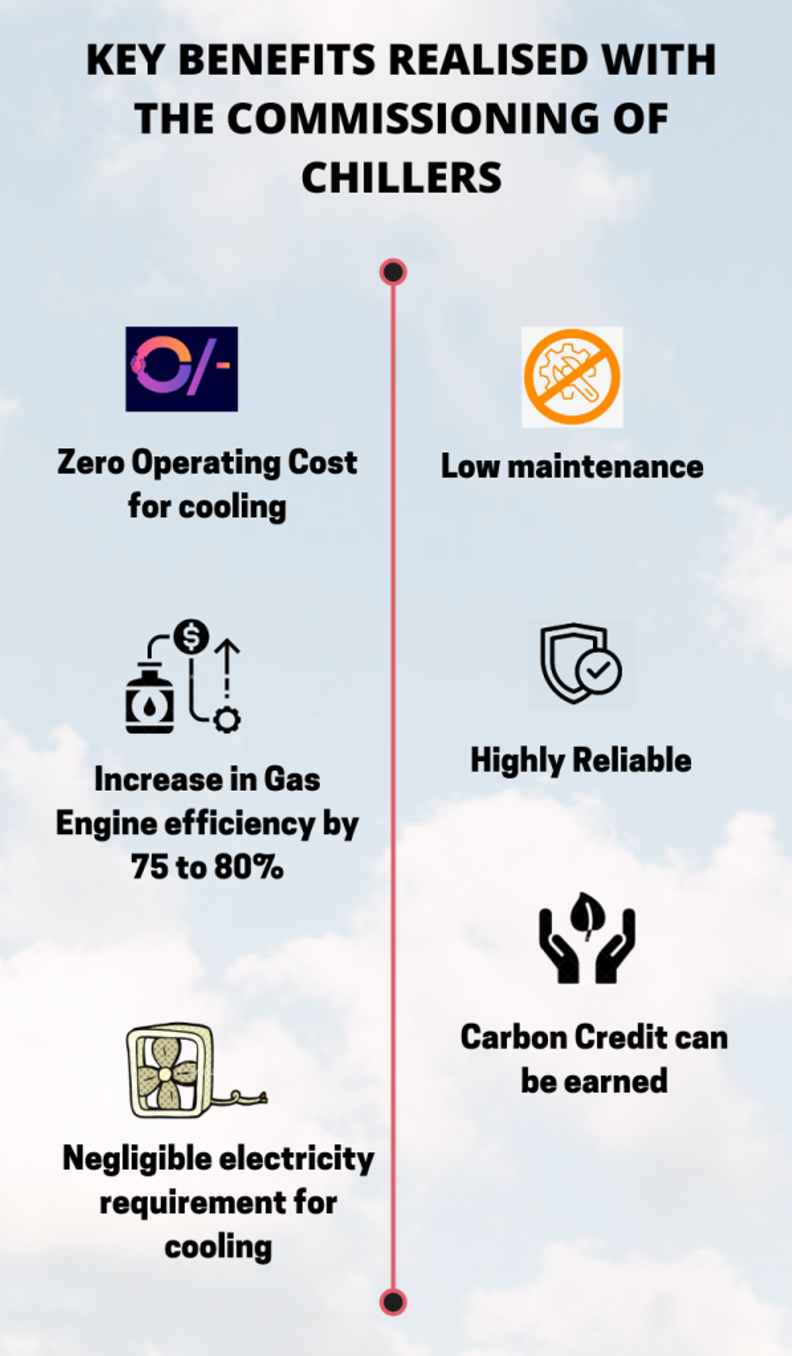
Through this collaboration with the yarn company, Thermax has not just met but exceeded energy efficiency aim of the textile giant. Owing to the reduction in electricity consumption, the energy savings for the company is highly impressive. Thermax’s absorption chillers have met the cooling needs of the mills in the most sustainable way while saving a huge margin in their operational costs.
Comments