Capacity enhancement of process condensers and heat exchangers
- coolingcommunicati
- Jun 24, 2016
- 2 min read
Crude oil Refineries and Petrochemical plants takes a planned shutdown every 3 to 5 years. During this shutdown most of the Process Condensers on the water side are opened and inspected.
On inspection heavy fouling and scaling is found both on the tubes and shell as well as in the inlet and outlet pipes.
The most common type of fouling is the precipitation of solid deposits in a fluid on the heat transfer surfaces. Another forms of fouling include corrosion and chemical fouling.
At times, heat exchangers also get fouled by the growth of algae in warm fluids. This type of fouling is called the biological fouling. Fouling represents additional resistance to heat transfer and causes the rate of heat transfer in a heat exchanger to decrease, and the pressure drop to increase. The fouling increases with increasing temperature and decreasing the fluid velocity.
Also, corrosion is a big issue at some places. The procedure for cleaning is to disassemble the heat exchanger, do chemical cleaning and assemble again. This process is time consuming and expensive too.
To resolve this issue two options are available:
a) To replace the Process condenser or Heat Exchanger with the new one: Replacement activity takes about 8-10 days which attracts substantial loss in revenues due to production loss. Shut down of the production process is mandatory.
b) To reduce the water temperature through the process condenser or Heat exchanger so that it operates at designed conditions:
Heat transfer enhancement is the practice of modifying a heat transfer surface to increase the heat transfer coefficient between surface and the fluid. High performance heat exchangers of a fixed size can give an increased heat transfer rate by decrease in temperature difference between the process fluids which enables efficient utilization of Thermodynamic availability.
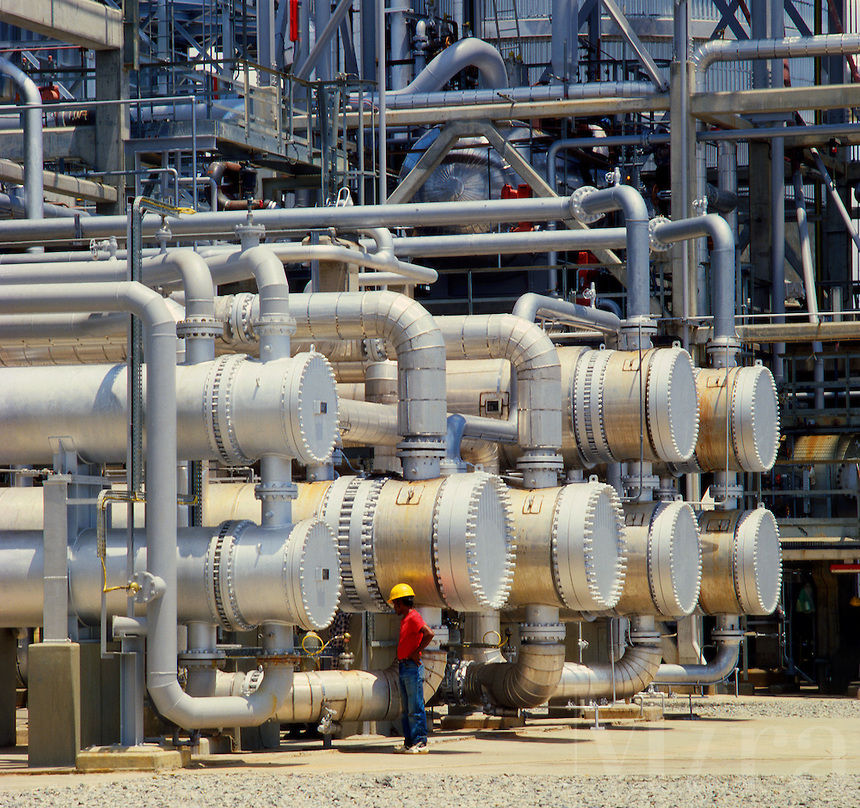
Process Improvement using Thermax Cooling solutions:
Thermax Absorption Chillers are installed to supply chilled water to Process Condensers or Heat Exchangers at lower temperature. By lowering the process water temperature, designed conditions of the process condensers can be achieved. The preferred chilled water temperature is in the range of 10-15 Deg C. Installation and piping for the Thermax Absorption Chiller is done without shutting down the plant by ‘Hot Tapping’ process. Thermax Absorption Chiller is a skid mounted device and it can be shifted from one plant to another. The chillers runs on waste heat available in the plant like low pressure steam or hot water.
Comentarios